D&G Machinery Helps Tangshan Customer Lead the New Era of Green Infrastructure
Recently, this DGXR3000Di Monoblock recycled asphalt mixing plant of D&G Machinery was officially put into operation in Hebei, mainly to help the construction of Tangshan municipal road projects. Faced with the triple pressure of soaring raw material prices, higher environmental protection thresholds, and tightening carbon emission constraints in the road construction industry, Tangshan Gangfa New Energy Development Co., Ltd. (hereinafter referred to as "Tangshan Gangfa") has solved the problem with innovation. Its recycled asphalt mixing plant, with its industry-leading 50% recycled material blending rate and intelligent warm mixing technology, has successfully solved the binary opposition between high-quality road construction and sustainable development, and provided a replicable solution for the infrastructure industry in trouble.
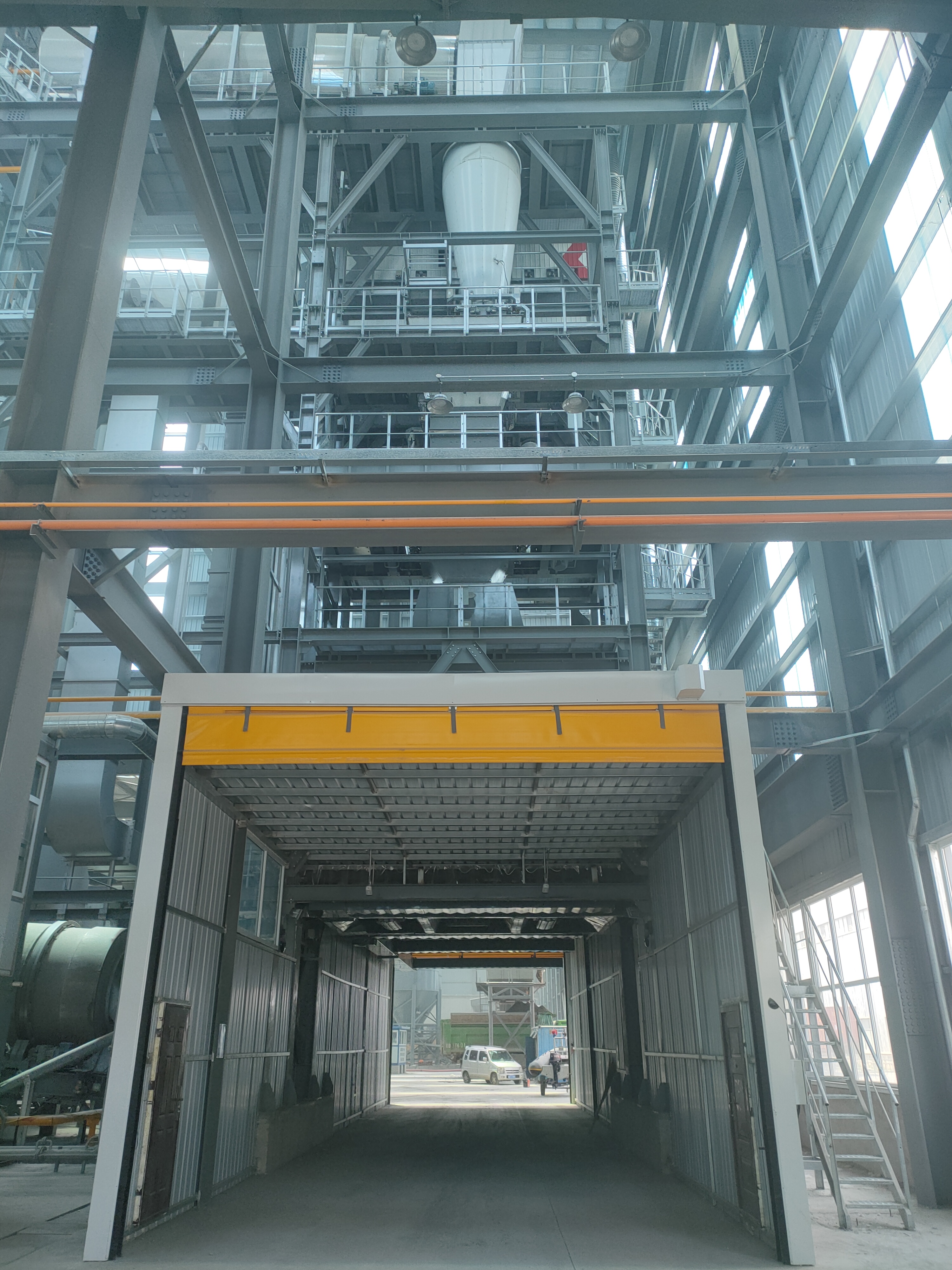
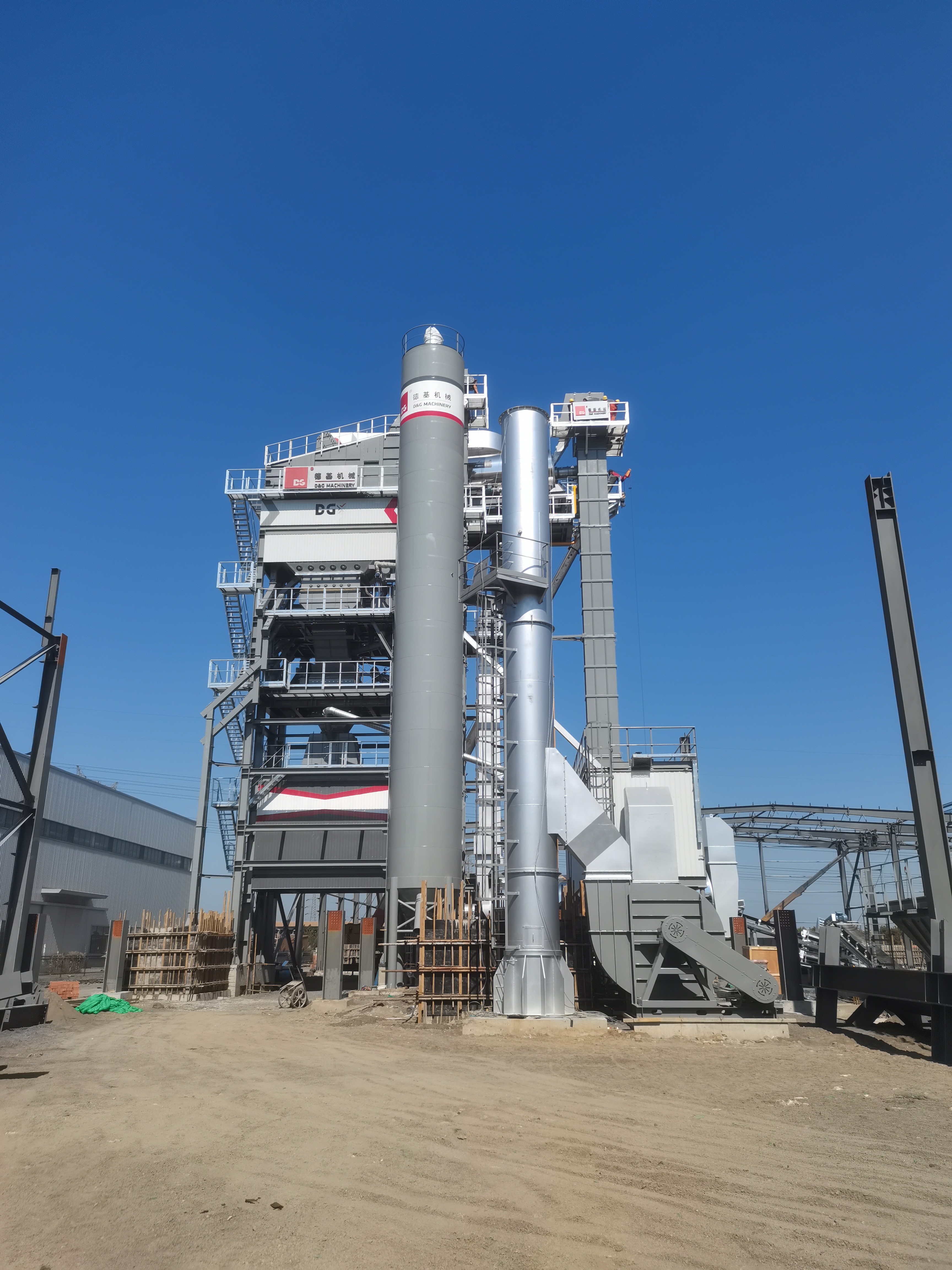
Equipment Highlights
1. High Efficiency Regeneration Technology
DGXR3000Di adopts the leading hot recycling technology of D&G Machinery, which can achieve a RAP mixing rate of up to 50%, significantly reducing the cost of raw materials and reducing resource waste. Its double drum design ensures that the new and old materials are evenly mixed, and the quality of the recycled materials is comparable to that of new materials.
2. Intelligent Control System
Equipped with the fully automatic "Feiyue Zhiyun" intelligent control management system, it can achieve accurate metering, temperature control and real-time monitoring of production data to ensure the stability of the mixed material quality. The intelligent diagnosis function can quickly troubleshoot and improve the operating efficiency of the equipment.
3. Excellent Environmental Performance
Integrated multi-stage dust removal system (gravity dust removal + bag dust removal), dust emission ≤20mg/m³, low noise design and closed structure effectively reduce the impact on the surrounding environment.
4. Modular and Flexible Configuration
The equipment adopts a modular design, which is easy to transport, install and expand later, and can adapt to different production capacity requirements. It is particularly suitable for Tangshan customer's diversified project scenarios.
Project Highlights
1. Responding to the "Dual Carbon" Strategy
As a regional environmental protection pioneer, Tangshan Port Development has promoted the recycling of waste asphalt pavement materials by introducing a recycled asphalt mixing plant. The project can reduce carbon emissions by about 15% annually, helping Tangshan's green transportation construction.
2. Large-scale Project Adaptability
The equipment will be used for road maintenance in Tangshan and construction of surrounding expressways. Its 3000-type large-capacity design can meet high-intensity construction needs, ensure the progress of key projects, and provide a practical case for the promotion of recycling technology in the Beijing-Tianjin-Hebei region.
Warm-mix Bitumen Foaming Device
1.Energy Saving and Emission Reduction
2.Warm mix technology reduces the construction temperature of asphalt mixture by 30~40℃, directly reduces fuel consumption by more than 30%, and reduces CO2 and harmful gas emissions, which is in line with Tangshan Port Development's environmental protection positioning.
3.Extending the Construction Window
Normal construction can still be carried out in low temperature environments, alleviating the tight construction schedule in northern regions in winter and improving the project's operating efficiency throughout the year.
4.Optimizing Mixture Properties
Warm-mix bitumen is easier to compact, reduces pavement porosity, enhances water damage resistance and durability, extends road service life, and reduces full-cycle maintenance costs.
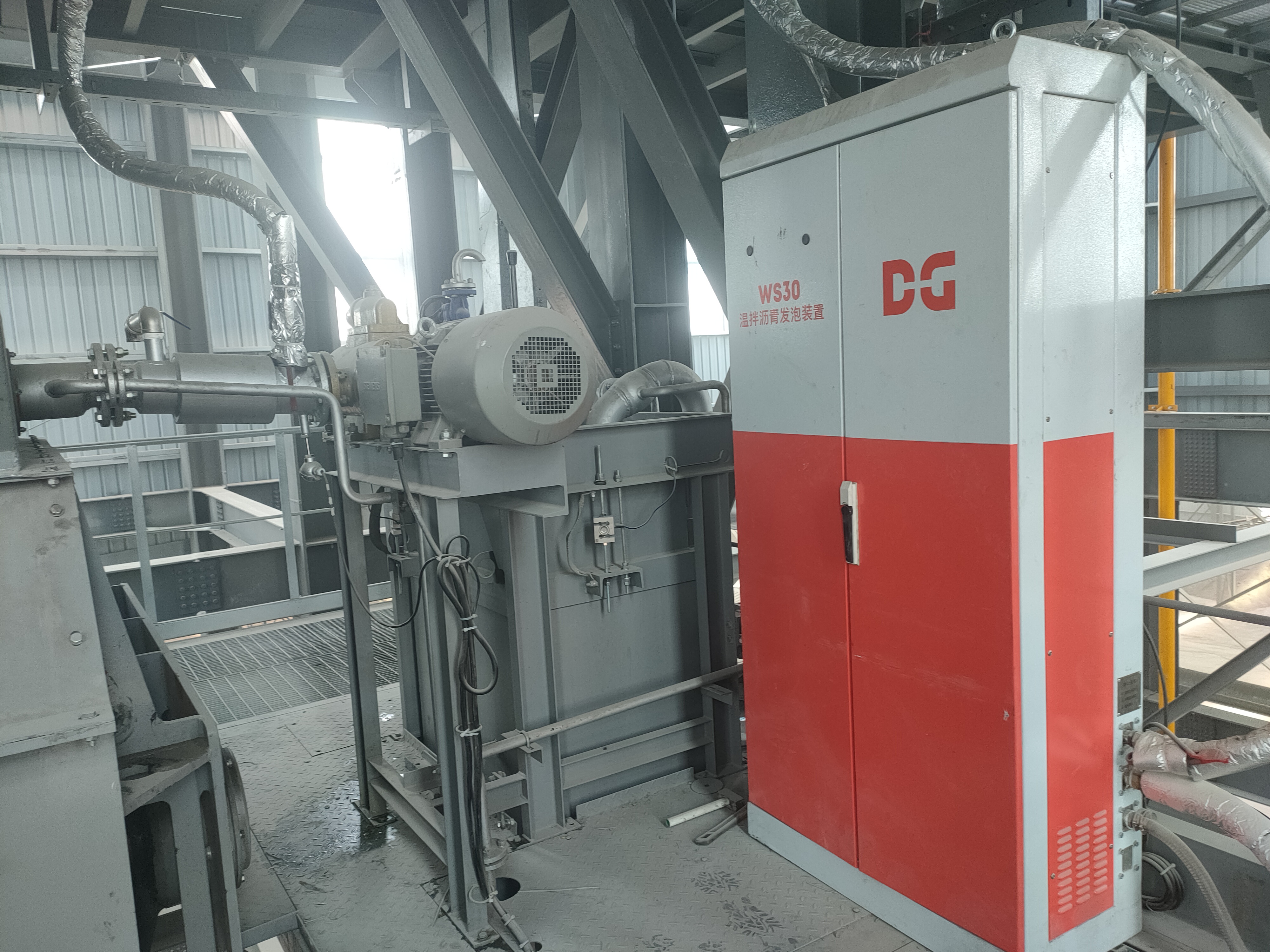
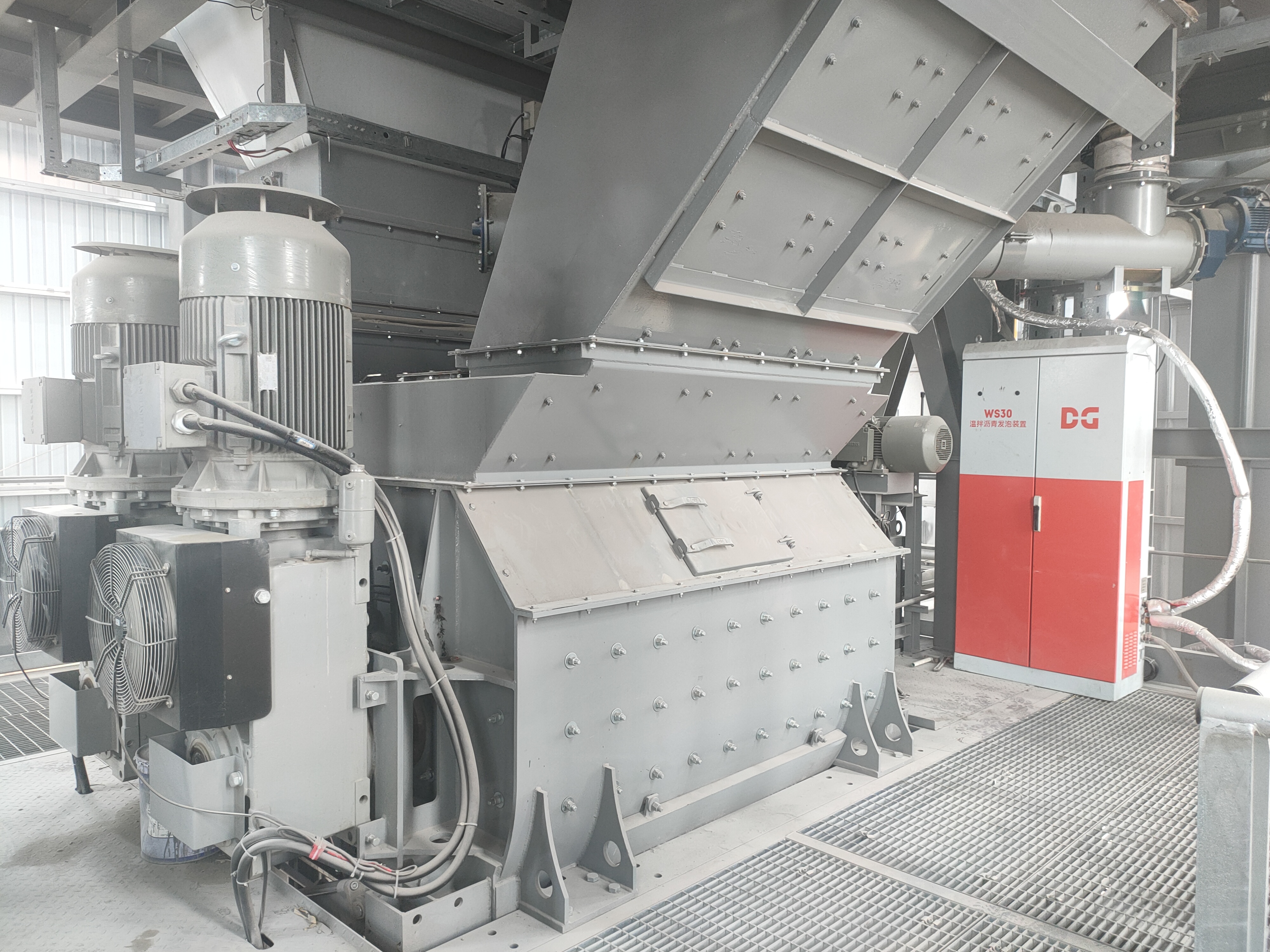
Tangshan customer achieved a win-win situation in economic and environmental benefits by introducing DGXR3000Di Monoblock asphalt mixing plant and warm-mix technology from D&G Machinery. This move not only enhanced the company's core competitiveness, but also demonstrated its innovative responsibility in the field of infrastructure, setting a new benchmark for the industry's green transformation.