How to Reduce Energy Consumption of an Asphalt Mixing Plant?
Strictly Control the Moisture Content and Particle Size of Cold Aggregates to Reduce Drying Energy Consumption
- 1) Site Hardening and Drainage:
- The ground of the aggregate yard should be hardened with concrete, with a slope above 3%. Drainage ditches and seepage wells should be set up around the yard to prevent rainwater infiltration.
- 2)Rain Shelter Coverage:
- Build a rainproof shed to cover the aggregates on rainy days, so as to avoid additional heating after getting wet.
- 3)Separate Storage Management of Fine Aggregates:
- Fine aggregates with a particle size of 0~2.36mm have the strongest water absorption capacity and should be stored separately and used preferentially.
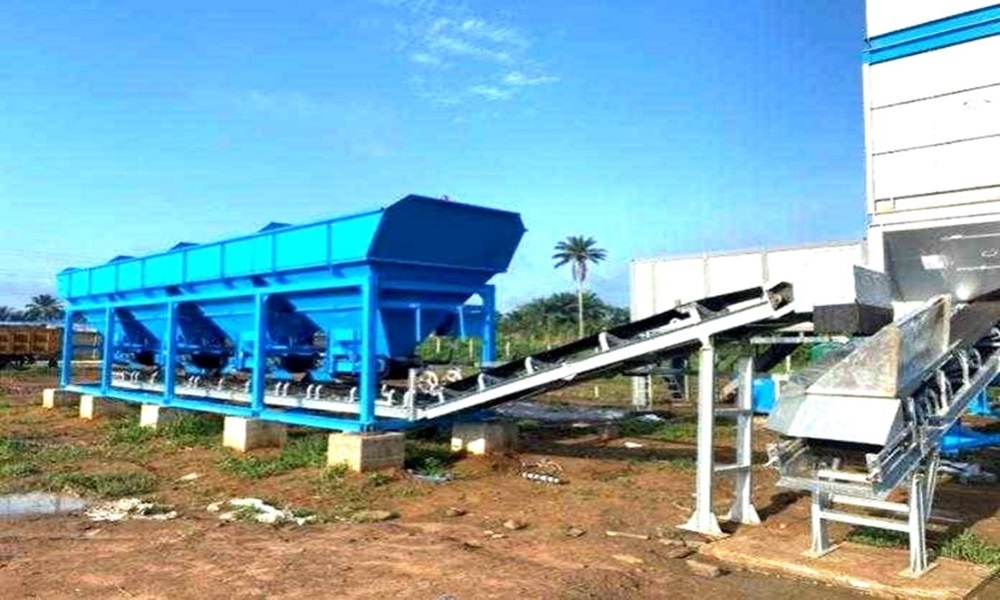
2. Aggregate Particle Size Control
A particle size qualification rate of less than 70% means an increase in the overflow rate. The overflow would result in fuel waste in the drying and screening process. Here are the countermeasures:
- 1)Pre-screening and Separate Storage:
- Use a vibrating screen for pre-screening. Aggregates of different sizes should be stored separately with concrete walls to reduce mixing.
- 2)Dynamic Adjustment of Feeding Speed:
- Monitor the particle size distribution through sensors and automatically adjust the rotational speed of the cold feeder belt conveyor to lower the overflow rate.
- 3)Case Study:
- By adopting the measures above, the moisture content of the aggregates on an asphalt mixing plant decreased from 3% to 1.5%, resulting in a 12% drop in drying energy consumption.
Optimize the Combustion System to Improve Thermal Efficiency
1. Fuel Selection and Atomization Retrofit
- 1) Heavy Oil as the Primary Fuel, Diesel as Auxiliary:
- Heavy oil features a higher calorific value (42 MJ/kg) at lower cost (USD 410/ton cheaper than diesel). A supporting atomization equipment should be equipped.
2)Heavy Oil Heating and Filtration:
Heat the heavy oil to 80~90℃ by a hot oil coil. Install a dual-stage filter to prevent nozzle clogging.
3)Automatic Switching System:
Install a pneumatic three-way valve. Use diesel for ignition during startup, switch to heavy oil after stable operation, and switch back to diesel to clean the pipelines before shutdown.
2. Burner Upgrade and Air-Fuel Ratio Optimization
1)High-Efficiency Burners: Dual-frequency variable axial-flow medium-pressure burners with automatic air-fuel ratio adjustment can improve combustion efficiency by 20%.
2) Real-Time Monitoring and Adjustment: Use flue gas analyzers to detect oxygen content (target value: 3%~5%) and dynamically adjust the damper opening to prevent unnecessary heat loss.
3) Case Study:
After retrofitting the combustion system, a plant cut its heavy oil consumption from 8.5 kg/ton to 7.2 kg/ton, saving fuel cost by USD 71,170 annually.
Variable Frequency Technology
1. Motor Variable Frequency Retrofit
1) Variable Frequency Control of Exhaust Fan:Traditional exhaust fans operate at a constant power, but the actual load fluctuates significantly. After installing a variable frequency drive (VFD), the rotating speed can be automatically adjusted based on the temperature of the drying drum, saving energy up to 25%.
2) Linkage of Belt Conveyor and Mixer:
PLC programming is used to achieve "no material, no machine running," reducing idle running time.
2. Application of Soft Start Technology
1) Protection of Heavy-load Equipment:Use soft starters for screw conveyors and aggregate elevator to alleviate the impact of starting current, extend equipment life, and cut electrical energy loss.
2) Case Study:For a 3000-model asphalt mixing plant with a 110-kW exhaust fan and an annual operation of 6000 hours, the variable frequency retrofit resulted in an annual energy savings of 95,000 kWh, equivalent to an electricity cost savings of USD 9,112.
Full-Process Insulation Design to Reduce Heat Loss
1. Key Area Insulation
1) Drying Drum and Pipelines:Wrap with aluminum silicate fiber felt (thermal conductivity ≤0.035 W/m·K), the surface temperature dropped from 120℃ to 50℃.
2) Bitumen and Heavy Oil Tanks:Place polyurethane foam insulation layers to reduce the frequency of heating.
2. Insulation of Hot Mix Storage Bin
1) Double-Layer Silo Structure:Inner steel plate + outer rock wool insulation board, with a hot air circulation system installed at the top to prevent rapid temperature drops in the asphalt mixture.
2) Case Study:
After retrofitting the insulation of the hot mix storage bin for a plant, the stability of the discharge temperature improved, and the consumption of heavy oil per ton of mixture was lowered by 0.3 kg.
Refined Production Management
1. Preventive Maintenance
1) Daily Spot Checks:Focus on inspecting the filter bags (clean when the pressure difference >1500 Pa) and bearing lubrication (put lithium-based grease every 500 hours).
2) Quarterly Overhaul:
Calibrate the weighing sensors (error ≤±0.5%) and clean the mixing cylinder buildup (reduce drive power by 10%).
2. Smart Dispatching System
1) Vehicle Identification and Dispatching:Implement GPS positioning and license plate recognition technology to shorten the waiting time of transport vehicles and reduce equipment idle running.
2) Residual Material Recycling:
Install a weighing system to monitor the residual material in mixer trucks and reuse it after re-proportioning for lower-grade applications.